In the chemical and petrochemical sector, sealing seals play a crucial role in maintaining the integrity and safety of pipe systems and reactors that handle often corrosive chemicals and sometimes at high temperatures. The characteristics sought in seals for these sectors are specifically their resistance to chemicals, their ability to withstand high pressures and temperatures, and their durability under demanding operational conditions.
SPECIFIC
APPLICATIONS

Chemical Reactors
O-Rings, usually made of FFKM, PTFE, or EPDM, are the best choice for withstanding high pressures and temperatures, as well as resisting the corrosion of chemical reactants.
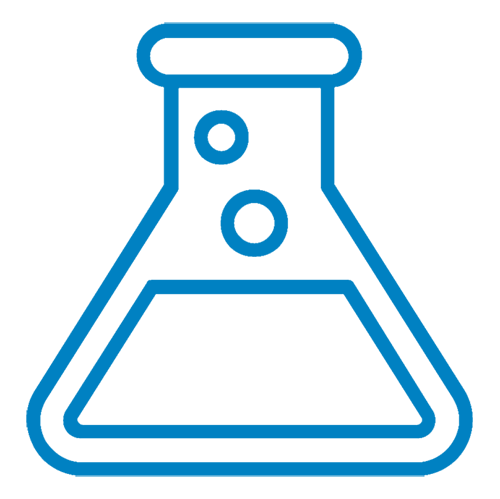
Heat Exchangers
The O-Rings, commonly made of EPDM, must prevent fluid leaks while withstanding temperature and pressure variations within the heat exchangers.
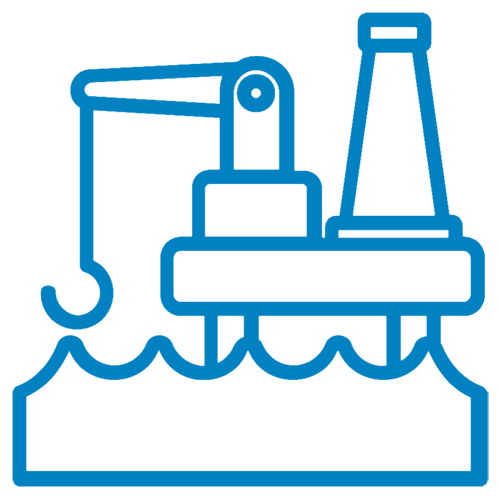
Pumps and Valves
Viton O-Rings are known for their excellent resistance to chemicals, maintaining the integrity of connections in pumps and valves that regulate the flow of chemicals.
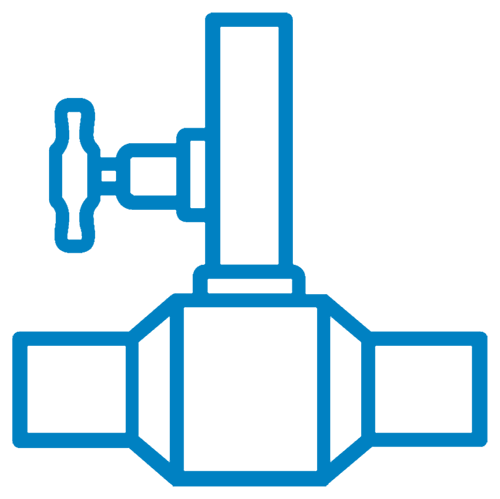
Piping Systems
O-Rings, preferably made of EPDM and PTFE, ensure secure connections between sections of pipe, preventing leaks and cross-contamination in the pipes.
APPROPRIATE MATERIAL
TYPES
- PTFE (Teflon): Highly valued for its exceptional chemical resistance, as well as its ability to withstand a wide range of temperatures. It is ideal for applications involving acids, bases, and organic solvents.
- EPDM (Ethylene Propylene Diene Monomer Rubber): Good for applications where diluted acids and other less aggressive chemicals are handled. It has good resistance to heat, ozone, and weathering.
- Viton (Fluoroelastomer): Extremely resistant to high temperatures and a wide variety of chemicals, including oils, solvents, and concentrated acids. It is particularly useful in environments that demand the highest chemical resistance.
- FFKM (Perfluoroelastomer): Offers superior chemical resistance, capable of withstanding extremely corrosive environments and high temperatures. Ideal for critical applications in the chemical industry.
- HNBR (Hydrogenated Nitrile Butadiene Rubber): Highly valued in the chemical and petrochemical sector for its resistance to heat, oil, and various chemicals. Its robustness makes it ideal for seals, hoses, and seals exposed to severe conditions.
COMMON
CERTIFICATIONS
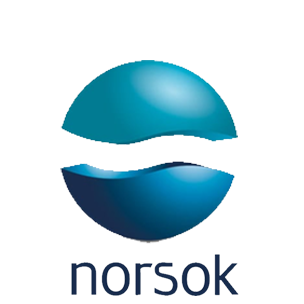
NORSOK
A common standard in the oil and gas industry, particularly for equipment used in severe environments. It evaluates the resistance of non-metallic materials to aggressive fluids, especially in the oil and gas sector.
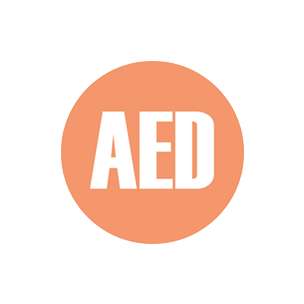
AED (Anti-Explosive Decompression)
This certification is crucial for seals used in conditions where rapid pressure changes can cause explosive decompression of the material. It ensures that AED seals can withstand these phenomena without losing their integrity.
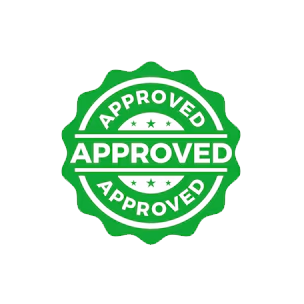
OTHER CERTIFICATIONS
- TOTAL FINA
- SHELL
- NACE TM0187
- Total Fina: The sealing seals that meet the specific requirements of Total Fina are designed to offer maximum performance and safety in oil and gas refining and processing operations, ensuring compatibility with the process fluids used by this company.
- Shell: Seals manufactured under Shell specifications resist corrosive environments and extreme working conditions, maintaining high efficacy in sealing and durability.
- Nace TM0187: This standard assesses the resistance of seals to stress corrosion cracking under environmental conditions similar to those found in oil and gas extraction and processing, ensuring that materials do not degrade under these stresses.